Common Tablet Defects by Parvez Officer QA
- Pharma Explorer
- Jul 9, 2021
- 2 min read
Updated: Nov 7, 2021
STICKING
Probable Causes
Punch face Condition
Excessive Moisture
Ambient Conditions (Temperature and Humidity)
Deficient Formulation and/or process
Punch tip worn, burred or have J-hook present
Insufficient compaction force
Common Corrective Actions
Polish puch face/consider matte finish
Check moisture content of granule
increase compaction force
Rework/replace punch
PICKING
Probable Causes
Punch face condion
Excessive moisture
Ambient condition (Temperature and Humidity)
Deficient Formulation and/or process
Punch tip worn, burred or have J hook present
Insufficient compaction force
Poor embossing design
Common Corrective Actions
Polish puch face/consider matte finish
Check moisture content of granule
Increase compaction force
Rework/replace punch
Redesign embossing (Consider pre pick islands and taper peninsulas of embossing)
LAMINATION
Probable Causes
Air entrapment
Excessive pre-compression
Exessive main compression
Ringed (worn) die bore
Punch tip worn, burred or have J hook present
Exvessive fines
Common Corrective Actions
Compress higher in die
Taper die
Reduce pre compression
Reduce main compression
Reverse or replace die
CAPPING
Probable Causes
Air Entrapment
Excessive pre-compression
Exessive main compression
Ringed (worn) die bore
Punch tip worn, burred or have J hook present
Exvessive fines
Common Corrective Actions
Compress higher in die
Taper die
Reduce pre compression
Reduce main compression
Reverse or replace die
SPLITTING
Probable Causes
Over compression
Poor granulation (Excessive fine, too dry)
Common Corrective Actions
Reduce pre-compression
Reduce main compression
Reduce fines
EDGE EROSION
Probable Causes
Unequal distribution of granulation in die bores
Particle segregation or stratification in hopper
Low moisture content
Poor tablet design
Poor compaction
Common Corrective Actions
Ensure raw materia quality
Balance/level tablet press
Set scrapper correctly
Minimize fill depth
Redesign tablet geometry
DISCOLORATION
Probable Causes
Excessive pressure
Poor tablet design
Frmulation component readily oxidized
Common Corrective Actions
Reduce main compression force
Evaluate tablet design
Identify discoloration and take action
DARK SPECS
Probable Causes
Dust, dirt or press lubrication in granulation
Excessive amount of lubrication on upper punch
Improper lubrication type on upper punch
Punch tip worn, burred or have J-hook present
worn die bore
Improper tip-to-die clearance
Common Corrective Action
Clean press more frequently
Use proper punch drip cups and key-way fillers
Rework/replace punches
Replace dies
Reevaluate die taper/upper punch penetration
SCORCHED BELLY BAND
Probable Causes
Excessive ejection force
Poor formulation
Common Corrective Action
Minimize depth of fill
Reformulate
Reduce lubricant blend time
Taper dies
CHIPPING
Probable Cuases
Punch tip worn, burred or have J-hook
Poor tooling design
Upper punch misalignment
Common Corrective Action
Rework/replace punches
Preload shaped tooling properly during installation
Inspect turret for excessive punch guide wear, key-way wear and die pocket wear
DOUBLE IMPRESSION (Round tablets only)
Probable Causes
Free rotation of either upper or lower punch
- After pre-compression - After main compression
- During tablet ejection
Common Corrective Action
Add keys on round puches
Use punch retainers/breakers
Probable Causes
Inconsistent lower punch bight
Granulation lost/gained after dosing
Over filling/under filled feeder
Worn improper scrapper adjustment
Non uniform lower punch lengths
Common Corrective Action
Check/replace lower punch retainer
Check/replace lower punch scrapper seals
Adjust feeder speed
Reduce recirculated powder
Chec/replace scrapper
Check lower punch working lengths
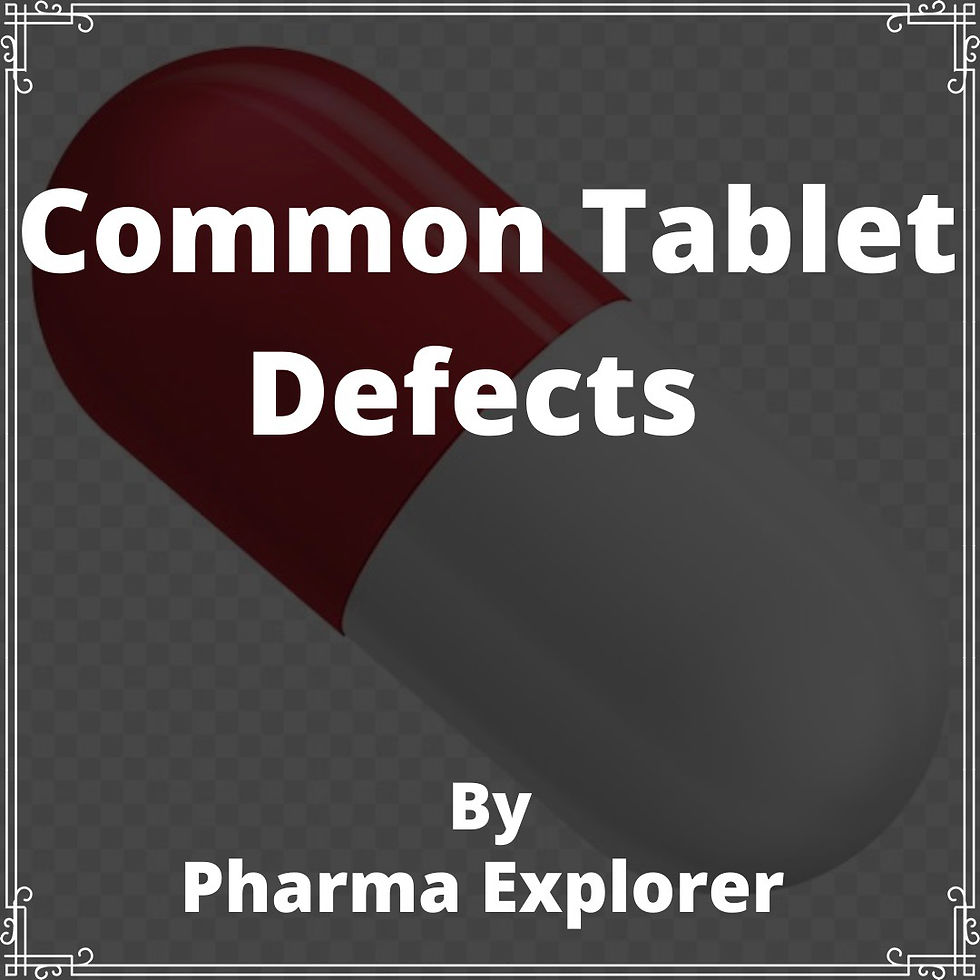
An article by Parvez
Thanks for reading. if you found this article valuable please share and subscribe.
for any suggestions email@Pharmaexplorer1@gmail.com
Read More 👇
Pharmaexplore.info
Comments